
Can you turn floppy fabric into a sturdy box? It's easy when you have the right bones...
Today I'm sharing all the useful stuff you need to know to make The Modular Fabric Box successfully.
Taking a look behind the scenes isn't always glamorous, but remember, supporting roles are essential!
So read on for links on where to get everything, to my tricks and secrets, you'll be even more inspired to sew yourself organised...
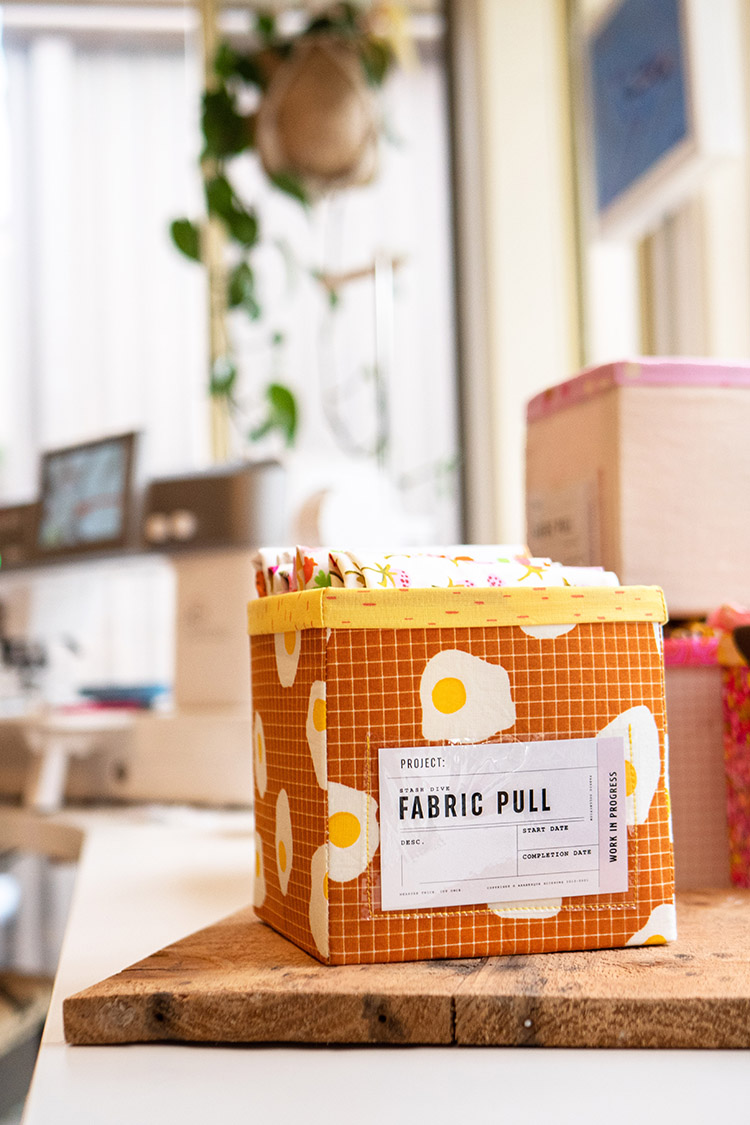
So let's break these boxes down bit by bit... so you can have that great feeling of hard work well done when you see a row of these in your cupboard and start making great use of the fabrics you already own.
Notions
The notions you'll need to make this are the usual crew...but there's a few extras you might not be so familiar with.
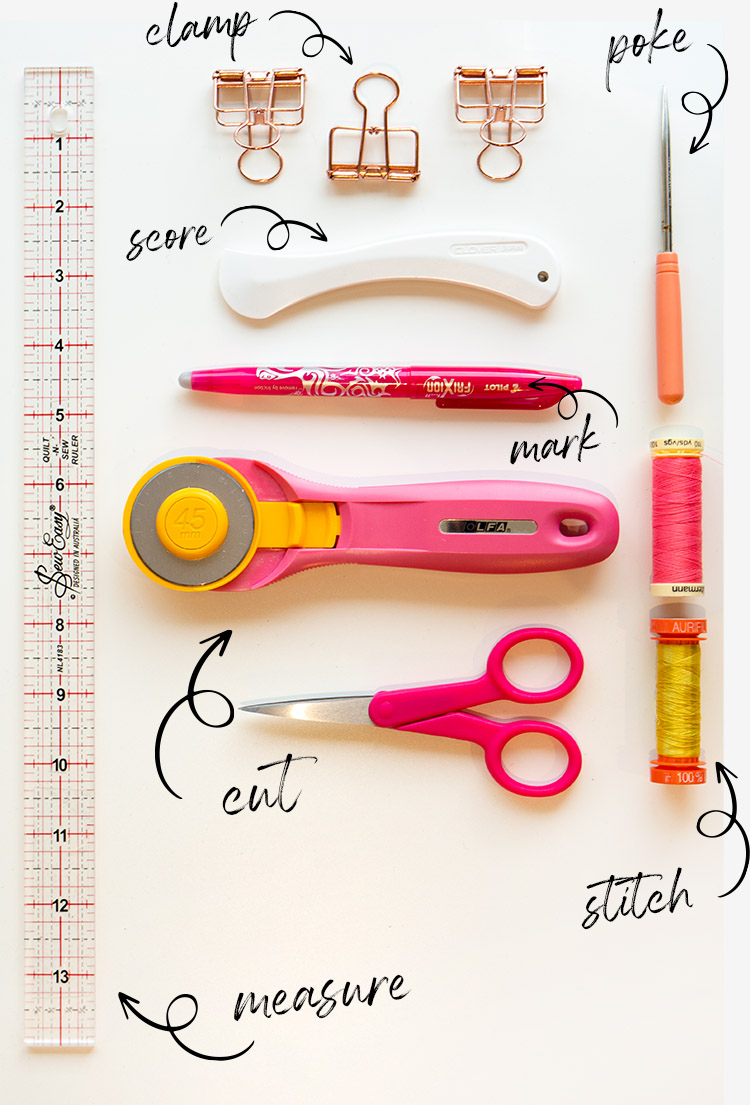
Let's talk about the weird tools.
A hera marker is used to score nice sharp creases in the sides, find one here as well. You can also use a butter knife for the same result.
An awl is used for poking holes for the rivet to go through, and the large clips are what I'm using to clamp the sides, and also hold the vinyl in place when sewing the pocket.
Regular binding clips are fine too, but might just be too short for some of it.
I don't recommend pins for this as they are really not strong enough to cope with the thicker layers.
Great Bones
The world of stabilisers and interfacing can be daunting at first, but they are really really useful in getting a great finish in the end.
They're not designed to be seen, but you can really see when they're not there.
For a great looking and functioning finished project, interfacing is essential.
To make this box rigid you'll need super stiff interfacing to give it support.
We're essentially turning floppy fabric into cardboard, or at least a cardboard-style stiffness.
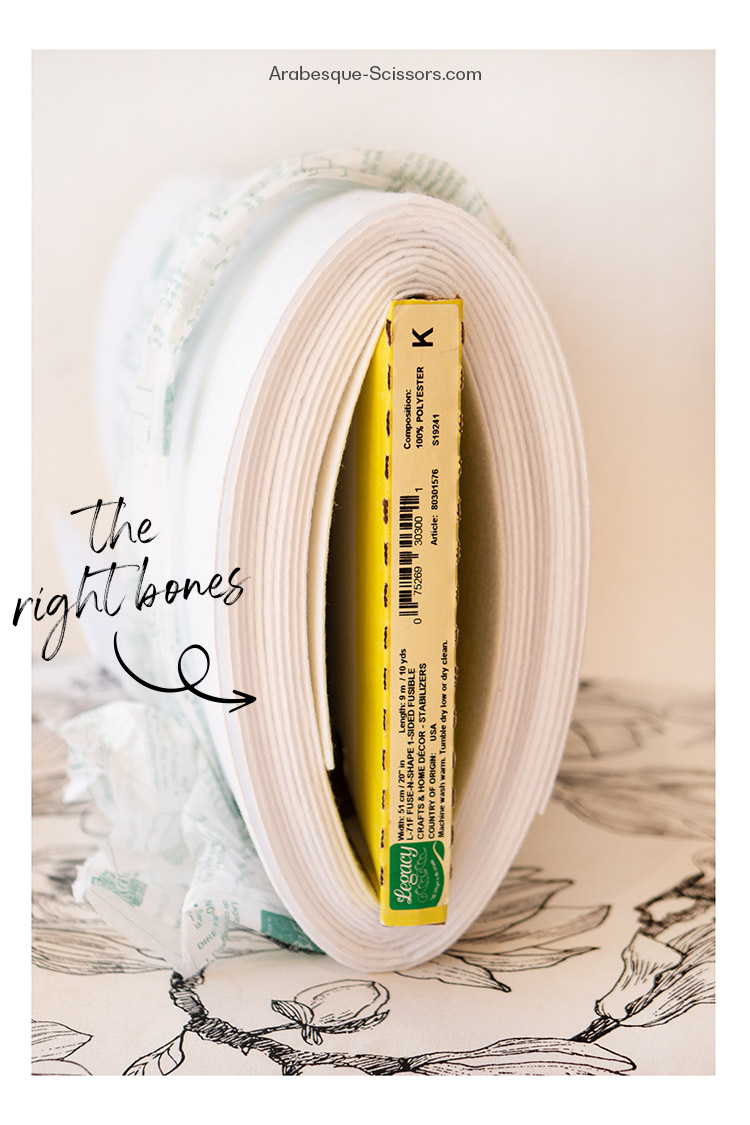
This box uses Fuse'n'shape (code 71F) by Pellon, (Legacy brand in Australia...all the codes are the same throughout the ranges.)
I like to buy a whole bolt because I'm making a huge lot of these, but you can also buy by the metre too.
The fusible part means that it bonds with heat from your iron, so that it glues to your fabric and makes it rigid.
There are some tips to know when fusing:
For this product you must use a pressing cloth.
You can't place the iron directly onto this product as it will melt.
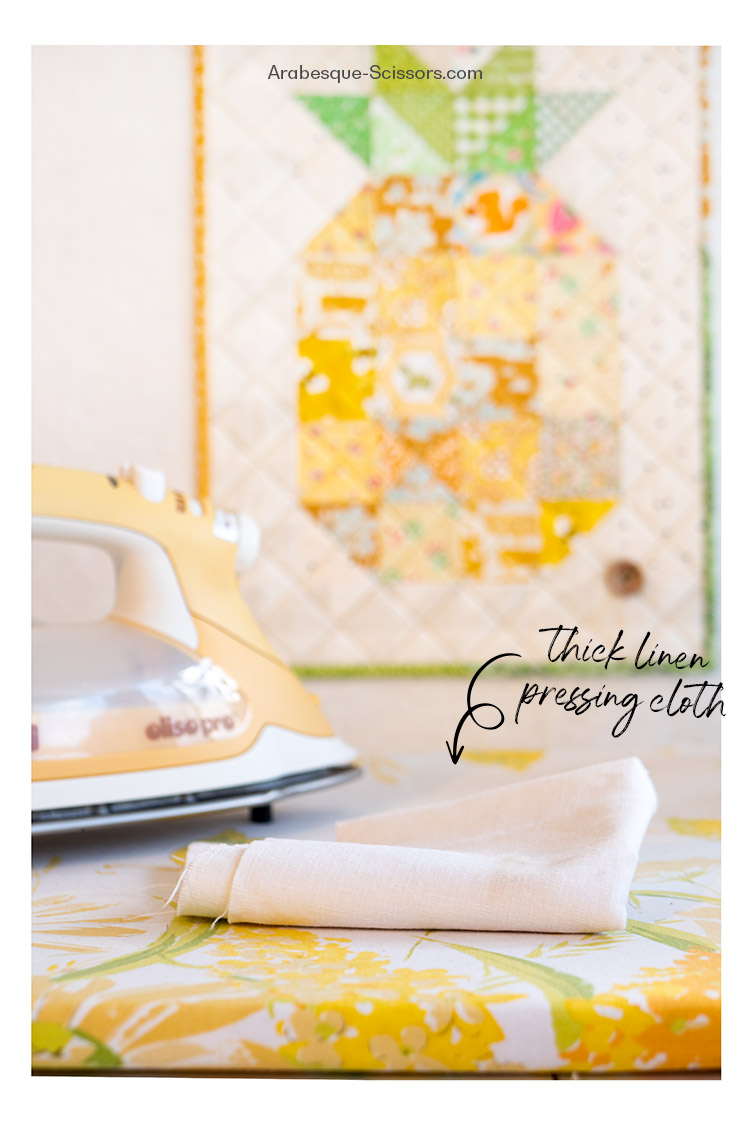
I keep a heavy-weight linen pressing cloth specifically for this, as linen can take the heat and is also the lowest lint fabric out there, which is a great bonus.
You can keep a dish towel especially for this if you wish.
Keep moving the iron as you go.
It takes time and a good bit of heat to get a good bond between the 71F and the fabric, so be patient.
But you do need to keep moving your iron every few seconds to avoid melting it. You can check how well it's fusing by gently tugging on the fabric every so often.
You want it really stuck there!
The benefits of using this are that it's thick, but not super bulky to fit under the machine or hard for the machine to sew through, so you don't need a heavy-duty machine.
You can also fold and squish it up to manipulate it under the machine, and then press it back into shape at the end again.
And just to restate it, you can't leave this stuff out if you want to make a box with structure.
All About Sewing Vinyl
Having a labeling system for these boxes just takes them to the next level.
I love the simplicity of the clear vinyl pocket, so let's talk about how to make it.
First, which kind of vinyl should you get?
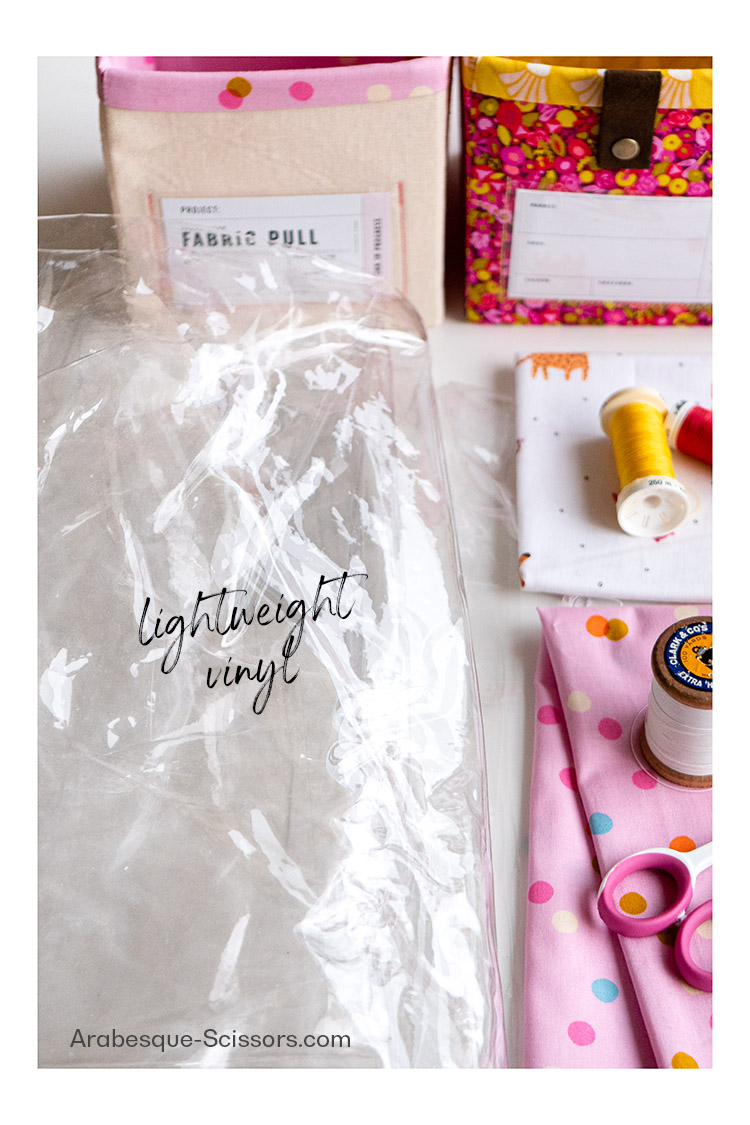
There are different types and weights of vinyl, so it's important that you get the right kind.
What we need here is the lightweight PVC version, typically about 0.2 mm or 4- 8 gauge thick.
There are a large range of beautiful colours, sparkles and even rainbow gradients out there.
But for this box to shine, you just need plain ol' clear vinyl so you can read the label.
If you're buying from a bag making supplier you don't need to worry too much about the weight, as they will have already picked sewing weight vinyl for you.
I got mine from Spotlight, and bought it from the vinyl tablecloth by-the-metre section. I found this was a good weight.
Be aware that you can't iron vinyl obviously, so try to store it flat or rolled.
If it is buckled, you can hold your iron above it and let the heat relax it flat again. Lying it out in the sun for a spell and using a hair dryer are also options too.
I find it a bit tricky to cut with a rotary cutter, only since it's clear it's hard to see where it is under the ruler.
So I like to mark sections with a permanent marker and then line those up with the quilting ruler to cut out.
If you've never sewn with vinyl before, there are a few things to be aware of...vinyl is sticky and won't feed through the machine easily with a regular foot.
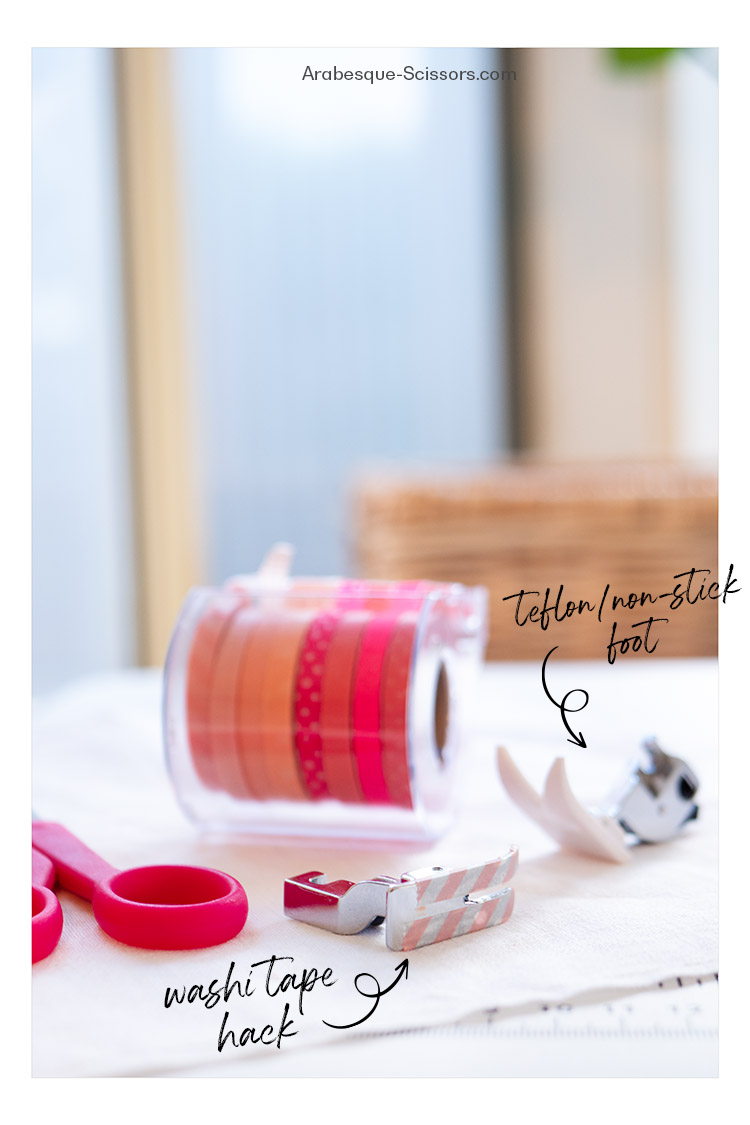
You can buy a purpose designed teflon or non-stick foot, or simply line the base of your foot with washi tape.
Watch me do this here for a cool hack that shouldn't cost you anything...
You only get one shot to sew vinyl, as the holes the needle punch in it are permanent, so try a practice run first so you get used to handling it.
I like to tape or clamp my vinyl pocket in place as I'm sewing it, as you can't pin through it obviously.
Leather Pulls & Rivets
These boxes feature a leather pull on the front fixed with a rivet that makes them look modern and edgy.
This is a totally optional step, but taking the time to finish the box off like this is totally worth it.
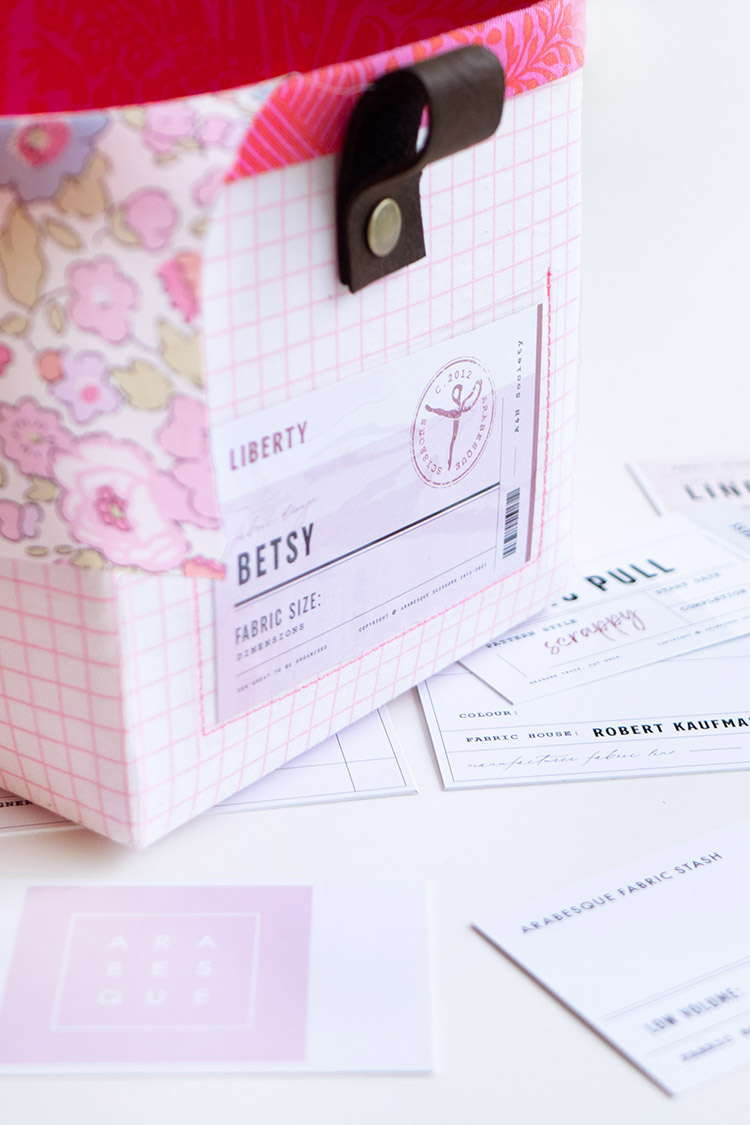
These boxes can now double as storage for other places in your house because they look so stylish.
It's makes them next level!
I've been cutting my own leather strips from a dressed hide that I've had for ages, and making the pulls for this, but faux leather or cork or even ribbon works great too.
You'll need a few tools to put the pull on the front, but nothing expensive.
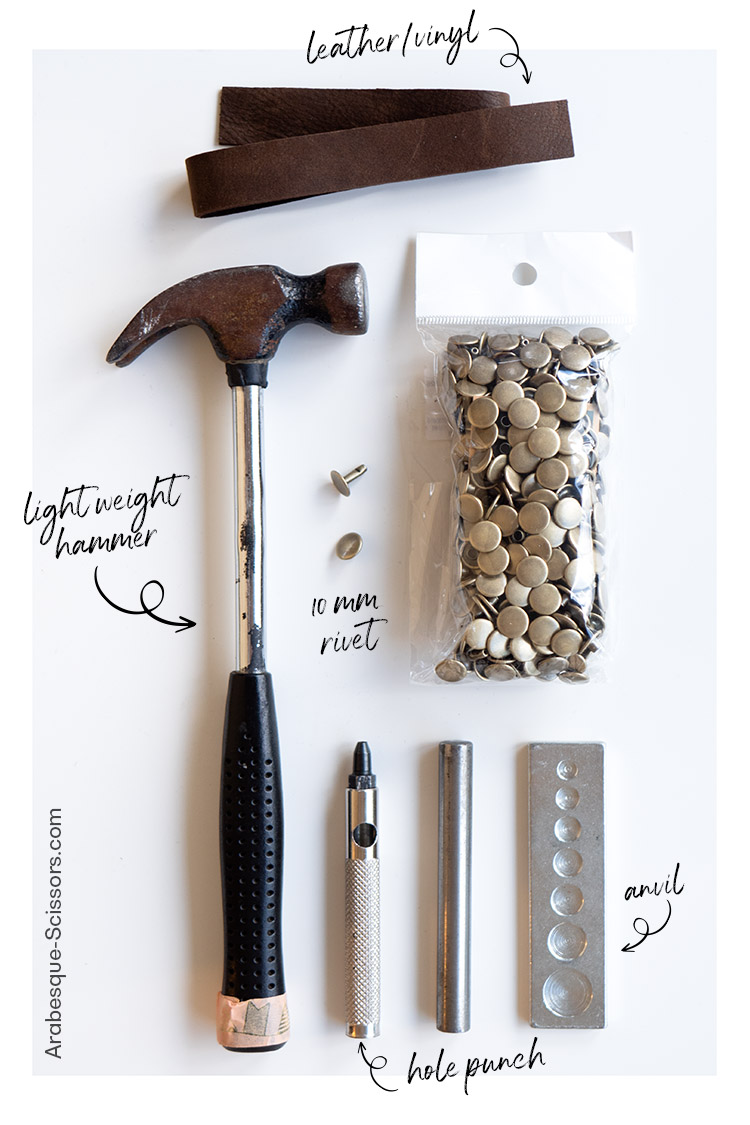
I have a scrapbooking hole punch, anvil and setter that I've had for years, and it works just fine.
I also use one of my kid's little hammers they had as small children. It's the perfect weight for this type of thing, and means you're wrangling the heavy duty hammer from the shed.
To prepare the box for the pull, mark the spot where you need to poke a hole through the box, then carefully push the awl through all layers, supporting the lining so it doesn't snag. You want a neat hole, not a big ladder in the fabric.
Then mark and punch a hole in each end of the leather strip and fold in half.
Push the long post of the rivet through the hole in the folded strip, then through the box and lining, and snap the backside of the rivet in place.
You may find depending on the length of your rivet post that you need an extra piece of leather as a spacer.
Set the rivet using the anvil and punch tools, until you feel the pull is firmly secured.
No Sew Hemming Options
Have you tried out this product yet??

Steam-A-Seam is an easy to use fusible tape that works so well for hemming when you don't want to sew.
I really recommend this in place of stitching the lining down, as the stitching can remove some of the crisp square corners on the box. Using a strip of this only takes a few seconds, but holds really well.
Labels
My favourite part of these boxes would have to be the custom labels.
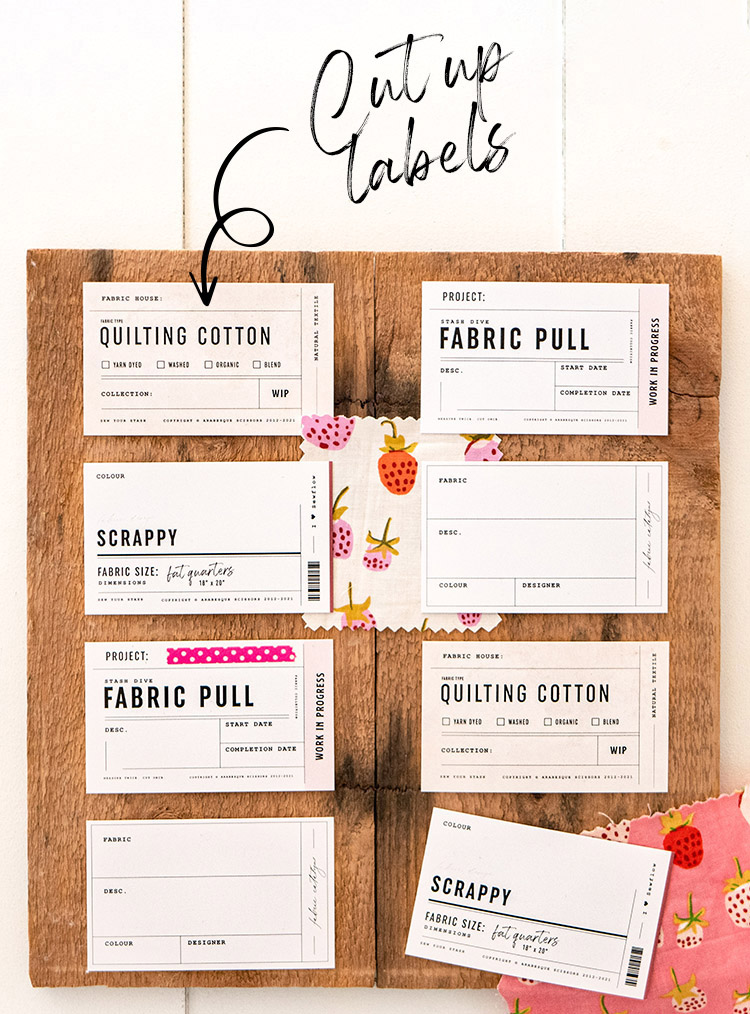
I had so much fun coming up with designs.
I've already added on to the original pattern with gift tag labels so that you can give these boxes as gifts.
If you've already purchased the pattern, give me a shout if you'd like these new ones too! For everyone else they're already included.
You can just print and cut these out using a regular-weight printer paper, but you'll get an awesome result if you use a heavier weight cardstock.
This usually still runs through a home printer just fine.
Don't cut them out with scissors either...just like fabric, paper benefits greatly from being cut with a craft knife and steel ruler, as you'll have no scissor marks or crooked edges.
Make sure to use an old cutting mat as a base for this tho - those craft knives will tear up a cutting mat in no time!
Final Pressing Matters
Getting a nice shape into your box at the end is the result of good pressing.
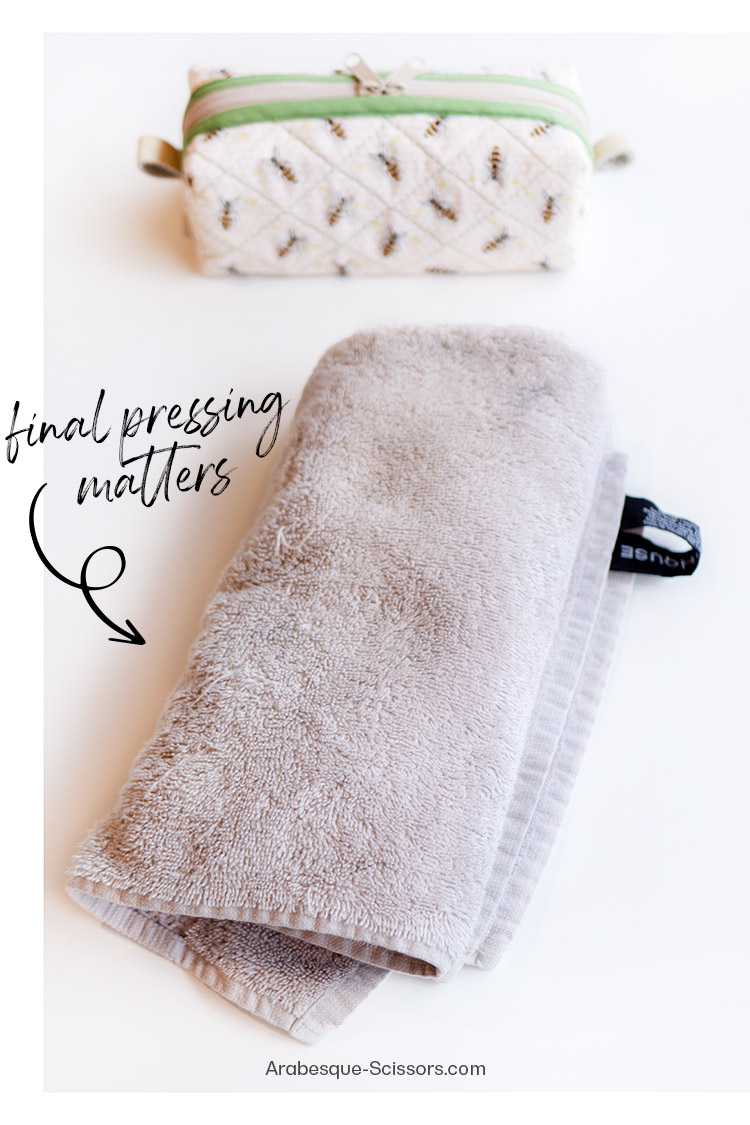
Use a thick old hand towel folded to roughly the same size as the dimensions of the box, and hold it as a support inside the box as you press the outside with the iron.
This will remove any of the creases you put there as you folded it under the machine.
Pinch the corners and edges as you go, as this will also help the box to sag less.
But as this is fabric, not cardboard, some sagging is to be expected.
So I hope you've found all these tips useful!
Don't forget to tag me when you make these...nothing makes me happier than to see you finding my patterns useful!
#ModularFabricGiftBox #TheModularFabricBox
Join my Facebook community
If you're a social bee, get involved with over 1100 sewists, quilters, and creators from around the world. Share your creations and get inspired!